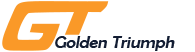
Industrial Sewing Machines: Types and Principles of Operation
Industrial sewing machines play a crucial role in the mass production of clothing, footwear, accessories, and other textile products. Unlike household models, these machines offer high-speed operation, long service life, and the ability to run continuously, making them ideal for industrial use. Below are the main types and operating principles of these machines.
Conclusion
Industrial sewing machines are characterized by their high speed, reliability, and versatility in working with various materials. Each model offers unique functionality, allowing for the efficient and rapid execution of a wide range of operations at different stages of garment and textile production.
The Process of Textile Production
The process of textile production encompasses various stages—from raw material processing to the final packaging of fabrics. For each of these operations, specialized equipment is used to ensure efficiency and high product quality.
Conclusion
Textile production encompasses many stages, and specialized equipment has been developed for each one to ensure both efficiency and high product quality. From the preparation of fibers to the packaging of finished products, every machine plays an important role in the creation of fabrics and textile goods.
The Process of Manufacturing Leather Products
The manufacturing process of leather products involves several key stages, each requiring specialized equipment to achieve high quality and durability. Below are the main production stages and the equipment used at each step.
Equipment Used in the Production of Leather Products:
Each stage of leather product manufacturing plays an important role in ensuring the high quality, durability, and attractiveness of the final products.
Sewing production involves numerous stages, each of which requires specialized equipment to ensure high-quality and efficient manufacturing. Below are the main types of equipment used at each stage.
In summary, the sewing production process comprises numerous stages, each requiring specialized equipment to achieve high-quality products and ensure efficient operations.
The Wool Processing Process is a multi-step procedure that includes several stages—from raw material preparation to the packaging of the finished products. At each stage, specialized equipment is used to ensure the quality and durability of wool products.
Equipment used in the wool processing process:
The wool processing process requires the use of various types of specialized equipment at each stage, enabling the production of high-quality wool products with the desired characteristics.
The Cotton Processing Process begins with raw material preparation and ends with the packaging of the finished products. This process includes several stages, each of which requires specialized equipment. Below is an overview of the cotton processing process, excluding the stages of spinning, weaving, knitting, dyeing, and finishing.
Equipment Used in the Cotton Processing Process:
The cotton processing process demands a high level of mechanization and specialized equipment to ensure quality and efficiency at every stage.
The Fabric Dyeing Process involves several key stages, each of which requires specialized equipment to ensure even and high-quality dyeing. Below is a detailed overview of the process, starting from raw material preparation and ending with the packaging of the finished product.
Major Types of Production Lines for Fabric Dyeing:
The fabric dyeing process is highly technological and requires meticulous control at every stage to guarantee the quality and durability of the dyed material. Depending on production needs, these technological lines can be either semi-automatic or fully automated.
The Fabric Production Process involves several key stages, each requiring specialized equipment to ensure the high quality of the final product. These stages include raw material preparation, spinning, weaving, fabric processing, and packaging of the finished product.
Main Types of Production Lines:
Production lines can be fully automated or semi-automated, depending on the type of product and production volume. This flexibility allows manufacturers to adapt to market demands and production needs.
Production Lines for the Manufacturing of Threads
Production lines for manufacturing threads include various stages and equipment that ensure the high-quality production of textile and sewing threads, yarns, and synthetic fibers. These lines can be adapted to process different types of raw materials and to produce threads with the desired characteristics.
Main Types of Production Lines
Conclusion
Production lines for threads can be fully automated or semi-automated depending on the scale of production and the requirements of the enterprise. These lines encompass equipment for every stage of production—from raw material preparation to the packaging of the finished product. The use of modern technologies, such as texturizing and automatic dyeing, enables the production of high-quality threads with the necessary characteristics for various sectors of the textile industry.
Production Lines for Clothing
Production lines for clothing play a key role in the mass production of textile products by ensuring efficiency, speed, and high product quality. These lines can be adapted according to the type of clothing, the level of automation, and the organization of the workflow.
Types of Production Lines
Production Process
Additional Technologies in Clothing Production
Conclusion
Production lines for clothing enable the efficient and rapid manufacturing of various types of garments—from knitwear to outerwear and sportswear. The level of automation can range from manual setups to fully automated complexes, allowing for flexible adaptation to different production needs and volumes. The integration of modern technologies, such as laser cutting and robotic systems, significantly improves the precision and quality of the final products.