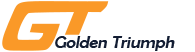
Machine Tools for Metal Processing: Types, Purpose, and Principles of Operation
Machine tools for metal processing are specialized equipment designed to perform various operations such as cutting, drilling, milling, turning, and grinding with high precision. These machines play a key role in manufacturing metal products that require quality and accuracy.
Main Types of Metal Processing Machines
Applications of Metal Processing Machines
Metal processing machines are widely used in various industries:
Advantages of Metal Processing Machines
Metal processing machines play an irreplaceable role in modern industry, ensuring high productivity and accuracy in performing complex metalworking operations.
Press Machines for Metallurgy: Types, Purpose, and Principles of Operation
Press machines play a crucial role in metallurgy, providing mechanical processing of metals through pressure and deformation. These machines perform key operations such as stamping, bending, forging, punching, and forming at various stages of metal product and component manufacturing.
Main Types of Press Machines for Metallurgy
Applications of Press Machines in Metallurgy
Advantages of Press Machines for Metallurgy
Press machines are an integral part of modern metallurgical production, ensuring efficiency and high-quality material processing.
Equipment for Metal Welding: Types and Purpose
Welding is the process of joining metal materials using heat, pressure, or a combination of both, requiring specialized equipment. Depending on the type of welding, materials, and quality requirements, various equipment is used to create strong and durable joints.
Each type of welding equipment is suited for specific processes and materials, ensuring high precision and strength of joints.
Equipment for Steel Processing: Types and Purpose
Steel processing involves a set of procedures aimed at modifying the physical and mechanical properties of steel to produce components with the required characteristics. Specialized equipment is used for these processes, playing a key role in ensuring precision, quality, and production efficiency.
Each type of equipment serves a specific role in steel processing, and the proper selection depends on the type of operation, required precision, and characteristics of the final product.
Metal Casting Equipment: Types and Purpose
Metal casting is a process in which molten metal is poured into a mold to create products with specified characteristics. This process is widely used in industries such as automotive manufacturing, shipbuilding, mechanical engineering, and construction. Metal casting equipment consists of several key categories, each performing a specific function.
Additional Processes and Equipment
Metal casting is a complex, multi-step process requiring precise equipment at every stage. Proper selection and use of these technologies enable the production of high-quality metal products that meet the stringent demands of various industries.
Metallurgical Furnaces: Types and Purpose
Metallurgical furnaces play a crucial role in ore processing and metal production, enabling smelting, refining, and metal enrichment while supporting various chemical processes. Depending on their purpose and processes, these furnaces can vary significantly from one another.
Main Types of Metallurgical Furnaces
1. Smelting Furnaces
Smelting furnaces are designed for melting metals and alloys.
2. Refining and Metal Processing Furnaces
These furnaces improve alloy quality and remove impurities from metals.
3. Regenerative Furnaces
Used for metal melting and processing in forging production.
4. Non-Ferrous Metal Smelting Furnaces
Designed for melting and processing non-ferrous metals.
5. Heat Treatment Furnaces
These furnaces alter the metal structure to improve mechanical properties.
Key Equipment for Metallurgical Furnaces
Metallurgical furnaces are essential for critical processes in metallurgy, and the choice of furnace type depends on the required operation and the type of material being processed.
Metallurgical Processing: Types, Stages, and Equipment
Metallurgical processing includes various methods through which metals undergo transformations to produce final products or intermediate materials such as ingots, rolled products, pipes, and wires. These processes involve smelting, forging, stamping, and other techniques that modify the physical and chemical properties of metals to achieve desired characteristics.
Stages of Metallurgical Processing
1. Metal Smelting
Smelting is the process of converting solid metallic materials into a liquid state, allowing for impurity removal, refining, and alloying.
2. Metal Casting
In this stage, molten metal is poured into molds, where it cools and solidifies into ingots or billets for further processing.
3. Pressing and Forging
These plastic deformation methods reshape metal under applied force without changing its volume.
4. Heat Treatment of Metals
Heat treatment involves heating and cooling metal to improve its mechanical and physical-chemical properties.
5. Metal Forming by Pressure
Stamping, rolling, and extrusion are primary methods for processing metals using compressive forces that lead to plastic deformation.
6. Welding and Soldering
Welding is used to join metal parts using heat, while soldering utilizes a lower-melting-point filler metal.
7. Grinding and Polishing
These processes refine metal surfaces, preparing them for further operations or improving their appearance.
Applications of Metallurgical Processing
Metallurgical processing is widely used in industries such as:
This process is essential for manufacturing structural materials, automotive parts, pipes, construction elements, and other metal products. Metallurgical processing helps maintain industrial standards, enhancing production efficiency and product quality.
Metal Processing Machines: Types, Purpose, and Principles of Operation
Metal processing machines are equipment designed to modify the shape, structure, and chemical composition of metals to produce final products such as sheets, profiles, wires, pipes, and other components. These machines play a crucial role in the metallurgical and manufacturing industries, where metals undergo various operations, including smelting, machining, forming, and cutting.
Main Types of Metal Processing Machines
1. Crushers
Crushers are used to break down metal waste or ore into the required fraction for further processing.
2. Metal Smelting Furnaces
Smelting furnaces are used to transform metals into a liquid state, allowing impurity removal and material preparation for further processing.
3. Press Machines
Press machines are used for plastic processing of metals, including forming, stamping, and drawing.
4. Sheet Bending Machines
Sheet bending machines are designed to bend metal sheets and strips into the required shape, essential for thin-sheet metal production.
5. Metalworking Machines
Machining equipment is used for precise processing of metal workpieces, including milling, turning, drilling, and grinding.
6. Metal Cutting Machines
Metal cutting machines are designed to cut workpieces into parts, allowing precise material separation.
7. Metal Welding Equipment
Welding machines are used to join metal parts by melting their edges and adding filler material.
Conclusion
Metal processing machines facilitate key operations in metallurgy and manufacturing, enabling efficient metal transformation into various products. From crushing and smelting to precision machining and welding, all these processes require specialized equipment to ensure products meet the necessary specifications while minimizing production costs.
Converters in Metallurgy: Types, Purpose, and Principles of Operation
Converters are essential devices in metallurgy used for smelting, refining, and altering the chemical composition of metals, primarily for steel production. Their main function is to oxidize carbon and other impurities in molten metal using oxygen, allowing for the production of steel with specific chemical and mechanical properties.
Main Types of Converters in Metallurgy
1. Blast Furnace Converters
Used for converting pig iron into steel by oxidizing carbon and other impurities such as manganese, silicon, phosphorus, and sulfur.
2. Bessemer Converters (For Pig Iron to Steel Processing)
Used in the Bessemer process, where oxygen is utilized to oxidize carbon and other impurities in pig iron.
3. Converters for Low-Alloy Steel Production
Designed for producing steel with added alloying elements such as nickel, chromium, and molybdenum.
4. Converters for Stainless Steel Processing
Used for producing stainless steel by purifying metal from carbon and other impurities while adding alloying elements such as chromium, nickel, and molybdenum.
Main Stages of Converter Operation
Conclusion
Converters play a crucial role in metallurgical production by enabling the production of steel with precise chemical and mechanical properties. The use of different types of converters allows for efficient metal refining, quality improvement, and parameter control, optimizing production and reducing the cost of the final product.
Automation of Metallurgical Processes: Implementing Technologies for Increased Production Efficiency
Automation in metallurgy involves the integration of advanced information technologies, software, and specialized devices to optimize and control metal production processes. The goal of automation is to enhance efficiency, improve product quality, reduce energy consumption, shorten processing times, and increase workplace safety.
Key Areas of Automation in Metallurgy
1. Automation of Metal Smelting Processes
2. Automation of Refining Processes
3. Automation of Casting Processes
4. Automation of Heat Treatment Processes
5. Automation of Cold Processing
Key Equipment for Metallurgical Process Automation
1. Automated Process Control Systems (APCS)
2. Sensors and Detectors
3. Programmable Logic Controllers (PLCs)
4. Robotic Systems
5. Intelligent Systems and Artificial Intelligence (AI)
6. Monitoring and Dispatching Systems
Advantages of Metallurgical Process Automation
Conclusion
Automation of metallurgical processes is becoming an integral part of modern metal production, helping to increase efficiency, improve product quality, reduce costs, and enhance workplace safety. The integration of advanced technologies, such as intelligent systems and robotics, significantly improves production processes and opens new opportunities for further industry development.