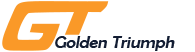
Equipment for the Production of Construction Blocks
1. Machines for the Production of Concrete Blocks
2. Machines for the Production of Aerated Concrete Blocks
3. Machines for the Production of Ceramic Blocks
4. Lines for the Production of Porous Blocks
5. General Equipment for All Block Types
Conclusion
Modern block production machines provide high automation, improving product quality and production efficiency. Each piece of equipment plays a crucial role, from raw material mixing to final packaging, enabling the production of various block types that meet construction standards.
Concrete Production: Technological Process
1. Preparation of Raw Materials
2. Mixing Components
3. Transporting the Mixture
4. Placement and Molding
Concrete is placed into prepared molds (formwork), which can be standard (walls, columns) or custom-designed for complex structures:
5. Curing Process
Concrete hardens through a hydration reaction between cement and water. Optimal curing conditions include:
6. Testing and Quality Control
7. Delivery and Application
Concrete is used in various construction projects, such as:
Types of Concrete
Conclusion
Concrete production requires strict adherence to technology at all stages – from raw material preparation to quality control – ensuring durability, safety, and efficiency in construction projects.
Concrete Production: Technological Process
Types of Concrete
Conclusion
The concrete production process requires strict adherence to technology at all stages – from raw material preparation to quality control of the final product. This ensures durability, safety, and efficiency in construction projects.
Equipment for the Production of Building Materials
Conclusion
Production lines for building materials involve a variety of machines and systems that ensure high quality and efficiency at all stages, from raw material preparation to final product packaging. Equipment selection must be tailored to the material type and production process to achieve optimal results.
Equipment for the Production of Paints and Coatings
Conclusion
The production of paints and coatings requires specialized equipment to ensure high-quality products at every stage. From raw material preparation to packaging, each process demands precision machinery to meet market standards and customer expectations.
Construction waste recycling is an important process for reducing environmental impact and reusing materials in construction. This process includes several stages, such as collection, sorting, crushing, and recycling of concrete, wood, metals, and plastics. Let’s consider the equipment for each stage.
At the first stage, waste is collected and sorted by material type. This allows useful components to be separated from debris and directed for recycling.
Equipment:Crushing is a key process for recycling concrete, bricks, and other hard materials. It helps reduce waste size and prepares materials for reuse.
Equipment:Recycled concrete from construction waste can be used as aggregate for new concrete mixtures.
Equipment:Wood waste, such as wooden structures and panels, can be recycled into various products or used as fuel.
Equipment:Construction waste often contains metal elements, such as reinforcement in concrete or metal structures. These materials can be recycled and reused.
Equipment:Plastic materials, such as packaging, pipes, or insulation, can be recycled for reuse in construction products.
Equipment:Construction waste recycling requires various equipment to efficiently extract, grind, and process different materials such as concrete, metal, wood, and plastic. This not only helps reduce waste volumes but also promotes the reuse of materials in construction processes, thereby conserving natural resources and reducing environmental impact.
Brick Manufacturing Process
Brick manufacturing is a multi-stage process that includes raw material preparation, molding, drying, firing, and packaging of the final product. Each stage requires specialized equipment to ensure quality and efficient production. Let’s take a closer look at the process:
Processes:
Methods:
Drying Methods:
Types of Kilns:
The firing temperature usually reaches 900-1000°C, necessary for achieving strength and resistance to external conditions.
Cooling Methods:
Packaging Methods:
Types of Bricks Depending on composition and purpose, several types of bricks can be distinguished:
Conclusion Brick manufacturing is a complex technological process that includes raw material preparation, molding, drying, firing, cooling, and packaging. Specialized equipment is used at each stage, ensuring products meet required quality standards. Modern brick factories use automated production lines, increasing efficiency and accuracy in manufacturing.
Cement Production Machines
Cement production lines consist of several key stages that require specialized equipment to ensure efficient and high-quality manufacturing. Let's examine the main stages and the equipment used at each step.
Equipment:
Equipment:
Equipment:
Equipment:
Equipment:
Equipment:
Conclusion Cement production lines include multiple stages, from raw material crushing to packaging the final product. Using specialized equipment at each stage ensures high-quality cement and efficient manufacturing processes.
Tile Manufacturing Lines
Tile manufacturing lines, whether for ceramic, porcelain, or glazed tiles, consist of several key stages. Each of these requires specialized equipment to ensure high-quality products. Let's explore the main stages of tile production.
Equipment:
Equipment:
Equipment:
Equipment:
Equipment:
Equipment:
Equipment:
Equipment:
Conclusion Tile manufacturing lines involve multiple essential stages, from raw material preparation to packaging. Using specialized equipment at each stage ensures high-quality tile production and improves manufacturing efficiency.
Asphalt Concrete Mix Production Technology
Asphalt concrete is a construction material consisting of a mixture of bitumen, aggregates (crushed stone, sand, and others), mineral powder, and additives. It is used for road surfaces, sidewalks, and other construction applications. The production process must consider the mix composition, technological features, and climatic conditions.
Types of Asphalt Concrete Mixes by Composition
Coarse-Grained Asphalt Concrete
Fine-Grained Asphalt Concrete
Sandy Asphalt Concrete
Types of Asphalt Concrete by Production Technology
Asphalt concrete mixes are classified into three types depending on laying temperature and production technology:
Hot Asphalt Concrete
Warm Asphalt Concrete
Cold Asphalt Concrete
Hot Asphalt Concrete Production Process
Component Drying
Component Mixing
Mix Storage
Advantages and Features of Cold Asphalt Concrete
Conclusion
The asphalt concrete production technology considers climatic and operational conditions, allowing its efficient use in various construction and roadwork projects. The appropriate production method is chosen based on the type of asphalt concrete, directly influencing its performance and durability.
Stone Ore Crushing
Stone ore crushing is a crucial stage in the processing cycle aimed at reducing the size of rocks and extracting valuable minerals for further beneficiation. This process efficiently prepares the ore for subsequent stages such as flotation, magnetic separation, or chemical enrichment.
Stages of Ore Crushing
Primary Crushing At the initial stage, large ore chunks are broken down into smaller fragments. The following machines are used:
The goal of this stage is to reduce ore chunk size to a few dozen centimeters, preparing the material for secondary processing.
Secondary and Tertiary Crushing At these stages, ore size is reduced to a few millimeters. The process involves:
These stages prepare the ore for fine processing and valuable component extraction.
Fine (Ultra-Fine) Crushing In the final stage, ore is crushed to sizes suitable for subsequent beneficiation processes such as flotation or chemical processing. The following equipment is commonly used:
Types of Crushers
Additional Processes To enhance crushing efficiency, the following processes are often implemented:
Purpose of Crushing The primary objective of ore crushing is to prepare material for further processing, such as:
The stone ore crushing process is essential for efficiently extracting valuable components from raw materials, forming the basis for further refining and high-quality metal production.